Mold Design
We offer professional injection mold design services tailored to your product requirements. Whether you’re starting with a sketch, a 3D model, or just an idea, our experienced design team will transform your concept into a fully manufacturable mold design.
Custom Injection Tooling Solutions Across Industries
CKMOLD brings extensive experience in plastic injection mold design, delivering tooling solutions that meet the exact needs of our clients across multiple sectors. Our designs are built to ensure high-quality, consistent production results.
We don’t just design molds—we design for efficiency, durability, and precision. Every mold is carefully engineered to optimize the injection process, reduce cycle time, minimize waste, and ensure the highest quality of final parts.
Simply share your specifications, 2D drawings, or 3D files, and we’ll provide a complete mold design solution, including:
DFM (Design for Manufacturability) analysis
Mold flow simulation (optional, based on project requirements)
Material and gate selection guidance
Cooling system optimization
Detailed 2D & 3D mold drawings
All designs are developed using industry-standard software such as UG/NX, AutoCAD, SolidWorks, and are fully compatible with global tooling standards like HASCO, DME, and Misumi.
Whether you need a simple 2-plate mold or a complex multi-cavity or family mold, CKMOLD is ready to support you from concept to production.
Let us help you build the foundation for a successful molding project.
Overmolding
Overmolding is an advanced injection molding process that combines two or more materials into a single, finished part. It enables manufacturers to enhance product functionality, improve grip or insulation, and achieve a sleek, high-quality appearance—all within a single molding cycle.
Insert Molding
Insert molding involves placing a pre-formed component, typically metal, into the mold before injecting plastic around it. This process creates a strong, integrated part that combines the durability of metal with the versatility of plastic—ideal for components like threaded inserts, connectors, and structural reinforcements.
Plastic Injection Molding
Plastic injection molding is the core of what we do at CKMOLD. This process involves injecting molten plastic into a custom-designed mold cavity to produce precise, repeatable parts at scale. We offer flexible injection molding solutions for a wide range of industries, ensuring high performance and consistent quality in every run.
Build Your Injection Mold in 3 Simple Steps
From idea to mold, we streamline the process—so you can focus on getting your product to market faster.
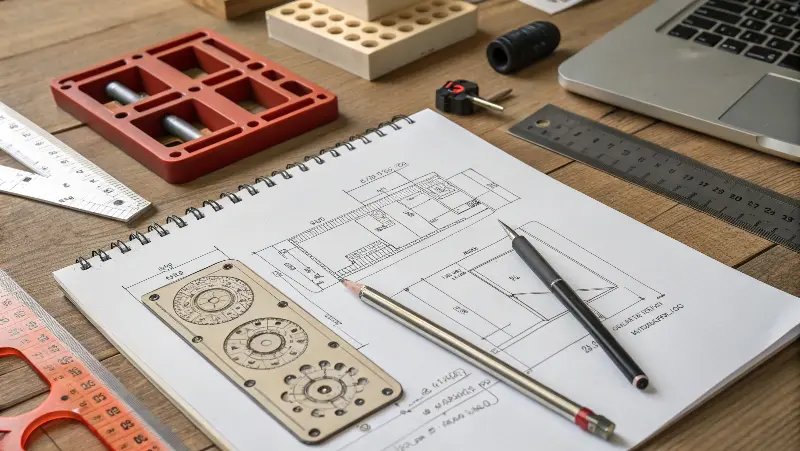
Step 1: Share Your Sketch or Sample
Send us your part drawing, concept sketch, or physical sample. This will serve as the foundation for our mold design and help us accurately capture your requirements.
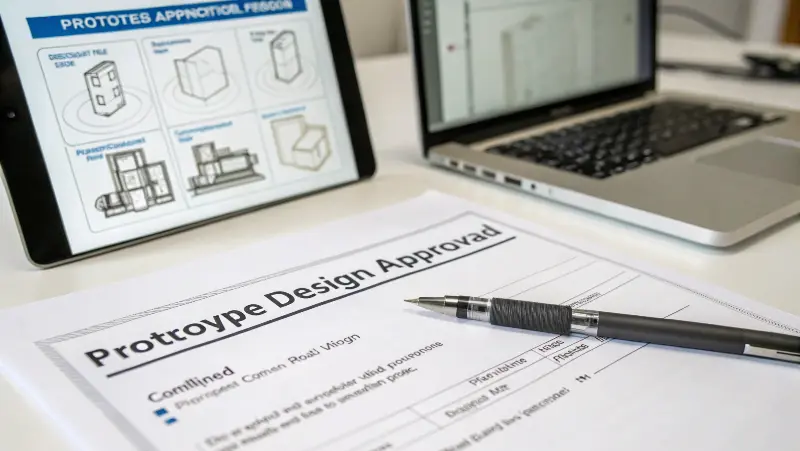
Step 2: Approve the Part Specifications
Once we’ve reviewed your specs, we’ll send them back for confirmation. Your approval lets us proceed with the initial mold design and prototyping.
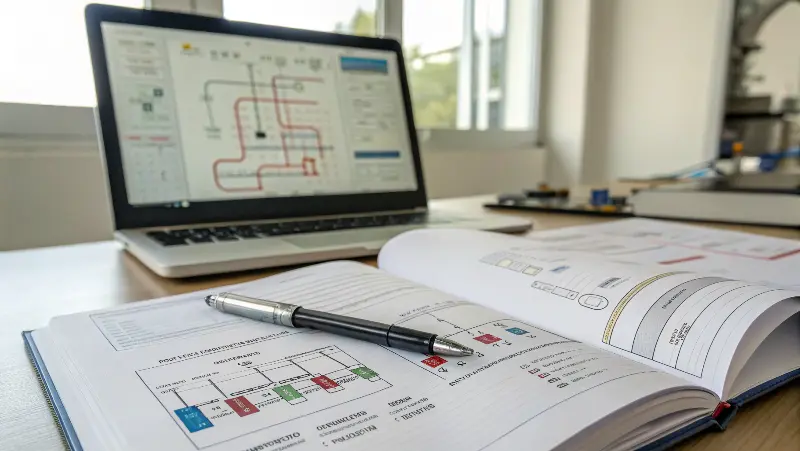
Step 3: Review & Confirm the DFM Report
We’ll provide a detailed DFM (Design for Manufacturability) report to ensure the mold is optimized for performance, cost, and production feasibility. Once approved, we’ll begin the tooling process.
Why Choose Custom Plastic Injection Mold Design at CKMOLD
Responsive Support, Anytime You Need It
At CKMOLD, our team is available 24/7 to support your project—from initial inquiry to final delivery. Whether it’s technical questions or project updates, we’re always just a message away.
Quick Quotes—Delivered Within 24 Hours
Need pricing fast? We provide accurate, detailed quotes within one business day, so you can move forward without delays.
Complimentary Design Revisions
Your satisfaction is our top priority. If adjustments are needed during the mold development phase, we offer free design revisions to ensure the final result meets your expectations.
Expert Mold Feasibility Review
Every mold design goes through a thorough professional analysis by our experienced engineering team. This helps prevent production issues, ensures part performance, and guarantees a smooth manufacturing process.
Popular Injection Mold Designs We Excel At
At CKMOLD, we offer a wide range of custom mold design services tailored to different industries. With years of experience and a commitment to precision, we deliver high-performance mold solutions that meet both functional and aesthetic requirements.
Automotive Injection Mold
CKMOLD provides precision mold design solutions for automotive parts, including bumpers, grilles, dashboards, and internal components. We ensure tight tolerances, excellent strength, and durability to meet the rigorous standards of the automotive industry.
Bucket Mold Design
We specialize in the design and manufacturing of high-quality bucket molds for industrial and household use. From paint buckets to food-grade pails, our molds ensure smooth surfaces, consistent wall thickness, and long mold life—ideal for high-volume production.
Storage Box Mold
Our storage box molds are widely used in home, office, and industrial settings. We focus on lightweight design, high efficiency, and long-lasting durability. Whether you’re producing small bins or large stackable boxes, we ensure easy release and strong structural integrity.
Toy Mold Design
We support global toy brands by providing safe, detailed, and child-friendly toy molds. From plastic figurines to interactive components, our designs prioritize material safety, dimensional accuracy, and colorful part compatibility for injection molding.
Plastic Chair Mold
As experts in plastic furniture mold design, we produce high-precision molds for a variety of chair styles—from stackable chairs to modern designer seating. Our molds deliver smooth finishes, strong structure, and high cycle life, suitable for both indoor and outdoor use.
Home Appliance Mold
CKMOLD designs and manufactures molds for plastic parts in home appliances, such as washing machine panels, refrigerator drawers, vacuum housings, and air conditioner vents. Our team ensures excellent fit, finish, and material compatibility to meet modern appliance standards.
Electrical & Electronics Mold
CKMOLD provides precision injection mold designs for electronic components and housings, including connectors, switch covers, enclosures, and cable management systems. Our molds are built to support high-volume production while maintaining excellent dimensional stability, insulation performance, and fine detail for complex parts.
Medical Device Mold
We offer high-precision mold solutions for the medical industry, where cleanliness, accuracy, and consistency are critical. Our medical molds are suitable for disposable items such as syringes, test tubes, diagnostic components, and casings for handheld devices. CKMOLD follows strict quality control protocols to meet industry-specific standards and ensure biocompatibility.
Expert Injection Mold Design Services in China
We specialize in delivering high-precision injection mold designs backed by years of hands-on engineering experience. Our in-house team of skilled mold designers and tooling experts works closely with each client to develop molds that match the exact geometry, function, and performance requirements of your product.
We design every mold with efficiency, accuracy, and longevity in mind. By recommending high-quality, wear-resistant materials and optimizing cooling, gating, and parting line designs, we ensure that each mold can withstand high-volume production cycles while maintaining consistent output and tight tolerances.
Whether you’re looking for a single-cavity prototype mold or a multi-cavity production tool, CKMOLD is your reliable partner for mold design and manufacturing in China.
Injection Mold Gate Design
The gating system is one of the most critical elements in injection mold design. A well-planned gate layout directly influences product quality, including surface finish, dimensional stability, and the presence of cosmetic issues such as weld lines, flow marks, trapped air, and warping.
At CKMOLD, we carefully design the gate type, location, and size to ensure smooth material flow and minimal defects, based on your part geometry and resin type.
Injection Mold Cooling System Design
An efficient cooling system is essential for reducing cycle time, improving part consistency, and increasing production output. Poor cooling can lead to extended molding cycles, increased costs, and product defects such as warpage or shrinkage.
At CKMOLD, we use advanced cooling layout strategies—including baffles, bubblers, and conformal cooling channels where applicable—to ensure uniform temperature distribution and optimal thermal management throughout the mold.
Injection Molding System Design
The overall molding system includes the configuration of the cavity, core, runners, and structural layout of the tool. A flawed design can delay mold fabrication, reduce efficiency, and negatively impact product aesthetics and performance.
Our engineering team at CKMOLD puts precision first—every detail, from parting lines to undercuts and venting, is optimized for functionality, mold longevity, and ease of manufacturing.
Ejection System Design
The ejection system is crucial for maintaining the integrity of molded parts. Improper ejection can lead to deformation, surface blemishes, cracking, or stress marks.
With over a decade of experience in mold engineering, CKMOLD ensures that all ejection systems—whether mechanical, pneumatic, or hydraulic—are designed for smooth part release with minimal risk of damage. We tailor the ejection design to each product’s geometry, material, and production volume.
Venting System Design
Proper venting is essential to ensure smooth injection and avoid common molding defects like burn marks, short shots, and trapped gas. When air or volatile gases are not effectively released during injection, they can cause serious issues with surface finish and part strength.
At CKMOLD, we carefully design and position venting grooves based on mold structure and material flow behavior, ensuring efficient air evacuation without causing flash or weakening the part.
Mold Material Selection & Durability
Choosing the right mold steel or base material plays a critical role in both performance and longevity of the mold. High-volume production tools require hardened steels like H13 or 1.2344, while prototype molds may benefit from more cost-effective materials like P20 or aluminum alloys.
CKMOLD always balances cost-efficiency and durability according to your production goals, resin type, and mold complexity—ensuring your mold delivers consistent results across thousands or even millions of cycles.
Complete Injection Mold Design Drawings & Engineering Workflow
we follow a structured, stage-by-stage engineering process to ensure seamless collaboration between design, tooling, and production teams. Each phase is carefully coordinated to deliver precision, efficiency, and reliability from concept to finished mold.
Here’s how our design and engineering process unfolds:
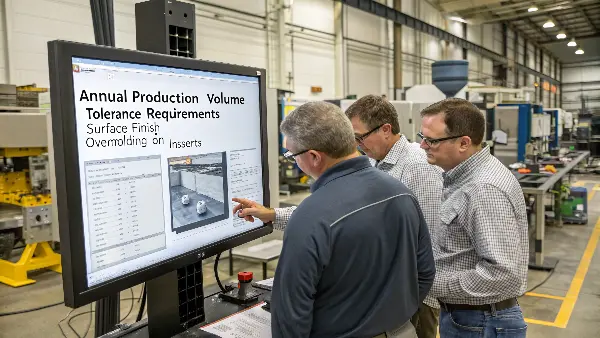
1. Project Kickoff & Requirement Review
We begin by thoroughly reviewing your part specifications—material type, annual production volume, tolerance requirements, surface finish, and any special features (e.g., overmolding or inserts). This ensures our mold design aligns perfectly with your production goals.
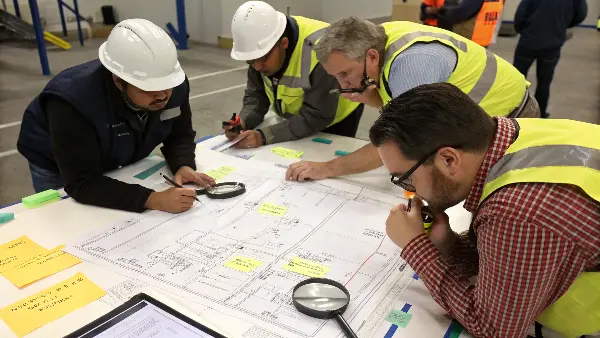
2. DFM Analysis (Design for Manufacturability)
Our engineers perform a detailed DFM review to identify and resolve potential manufacturing issues. This includes evaluating draft angles, wall thickness, undercuts, parting lines, shrinkage areas, and more. We provide suggestions to improve manufacturability and mold longevity.
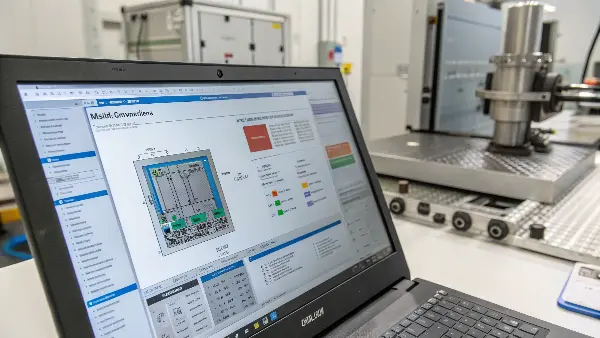
3. Mold Flow Analysis (Optional)
For complex parts or high-precision projects, we conduct mold flow simulations to analyze material flow, pressure distribution, weld line formation, air traps, and cooling behavior. This helps us optimize gate placement, venting, and cooling systems before cutting steel.

4. 2D & 3D Mold Design
Based on the confirmed product files and DFM report, we create complete 2D drawings and 3D mold structures. This includes design of the parting line, cooling channels, runner system, ejection system, sliders/lifters, and other functional elements.
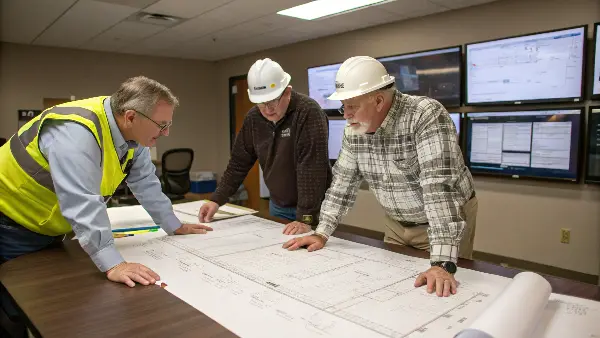
5. Internal Review & Client Approval
Once the design is complete, it undergoes internal cross-checking by senior engineers. We then send the drawings to you for approval. If needed, we host a design review meeting to walk you through the critical aspects before moving into production.
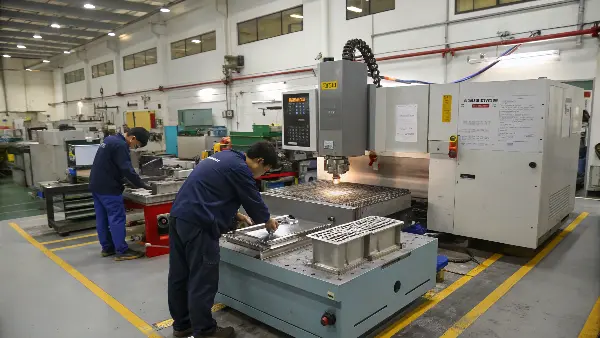
6. Mold Fabrication
After design approval, we begin mold fabrication. This includes steel purchasing, CNC machining, EDM, fitting, hardening, and final polishing. Our project managers oversee every step to ensure quality and on-time delivery.
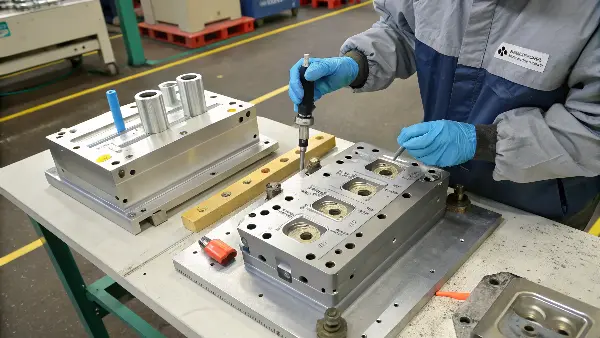
7. Mold Assembly & T1 Trial
The mold is assembled and tested with the first injection trial (T1). We evaluate part appearance, dimensions, and functionality to ensure it meets expectations. T1 samples are sent to you for feedback and approval.
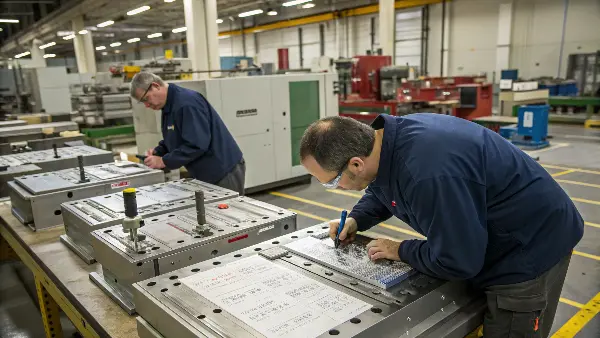
8. Final Optimization & Mold Shipment
Based on your feedback, we make any necessary adjustments (T2, T3…) until the mold performs flawlessly. Once approved, we conduct final quality checks, then prepare the mold for delivery or in-house mass production, depending on your needs.
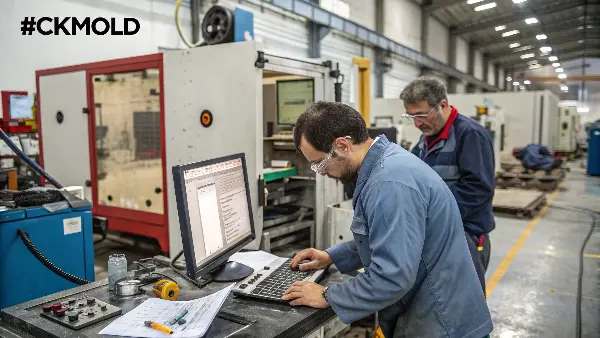
9. After-Sales Support
CKMOLD provides comprehensive after-sales support, including remote technical assistance, mold maintenance guidance, troubleshooting help, and repair services. We’re committed to supporting your production long after the mold is delivered.
Expert Plastic Injection Mold Designers Backed by 10+ Years of Industry Experience
Our mold design team is composed of highly skilled and experienced professionals who are passionate about delivering precision, performance, and innovation. With over a decade of hands-on experience, our designers are constantly exploring new technologies and design techniques to create molds that exceed customer expectations in both function and efficiency.
Our facility is equipped with advanced CAD/CAM software and high-precision tooling equipment, allowing us to streamline the design process and maintain tight tolerances throughout every stage.
We believe in collaborative design. Your feedback is vital to our process, and our engineers will keep you involved from initial concept to final approval. Whether you have specific molding ideas, unique part requirements, or detailed customization requests, we’re here to bring your vision to life—with accuracy, speed, and clear communication.