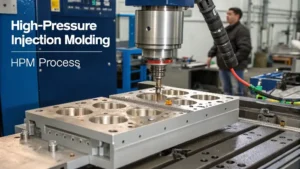
High Pressure vs. Low Pressure Injection Molding: Which is Right for Your Project?
Choosing between molding pressures feels complex? This decision impacts component integrity, cost, and production speed. Let’s simplify it. High-pressure injection molding uses higher forces (350-1300 bar) and temperatures (230-300°C) for complex, high-volume parts. Low-pressure molding uses gentler forces (1.5-40 bar) and lower temperatures (180-240°C), ideal for delicate electronics and overmolding.